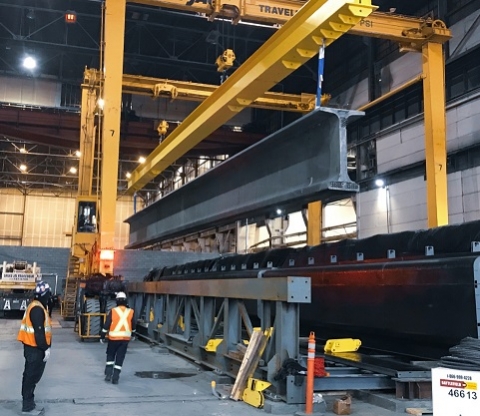
Pointe-Saint-Charles workshop is open
To move more quickly, several sections of the elevated structure (beams, arches, slabs, etc.) are fabricated at the plant and then assembled on site. Take a virtual tour of NouvLR's workshop at Pointe-Saint-Charles.
Prefabricating elements off-site allows teams to work on several things at the same time, prevents delays caused by weather conditions, but most importantly ensures high-quality products since the elements are designed and produced in a controlled environment.
Standard parts can therefore be prefabricated by Québec suppliers. This is the case, for example, with the company called Béton préfabriqué du Lac (BPDL), from the Lac St-Jean region, who was mandated with producing more than 4000 arches at their plant in Drummondville.
Non-standard parts, on the other hand, are fabricated at facilities specifically created for the project. NouvLR, the consortium in charge of building the REM, made the decision to setup a plant to prefabricate 276 NEBT beams in the Marc-Cantin Street sector of Montréal. The location was selected due to favourable logistics and to minimize impact on the road network. The beams will be installed nearby, beginning at the Lachine Canal, up to the Rive-Sud terminal station.
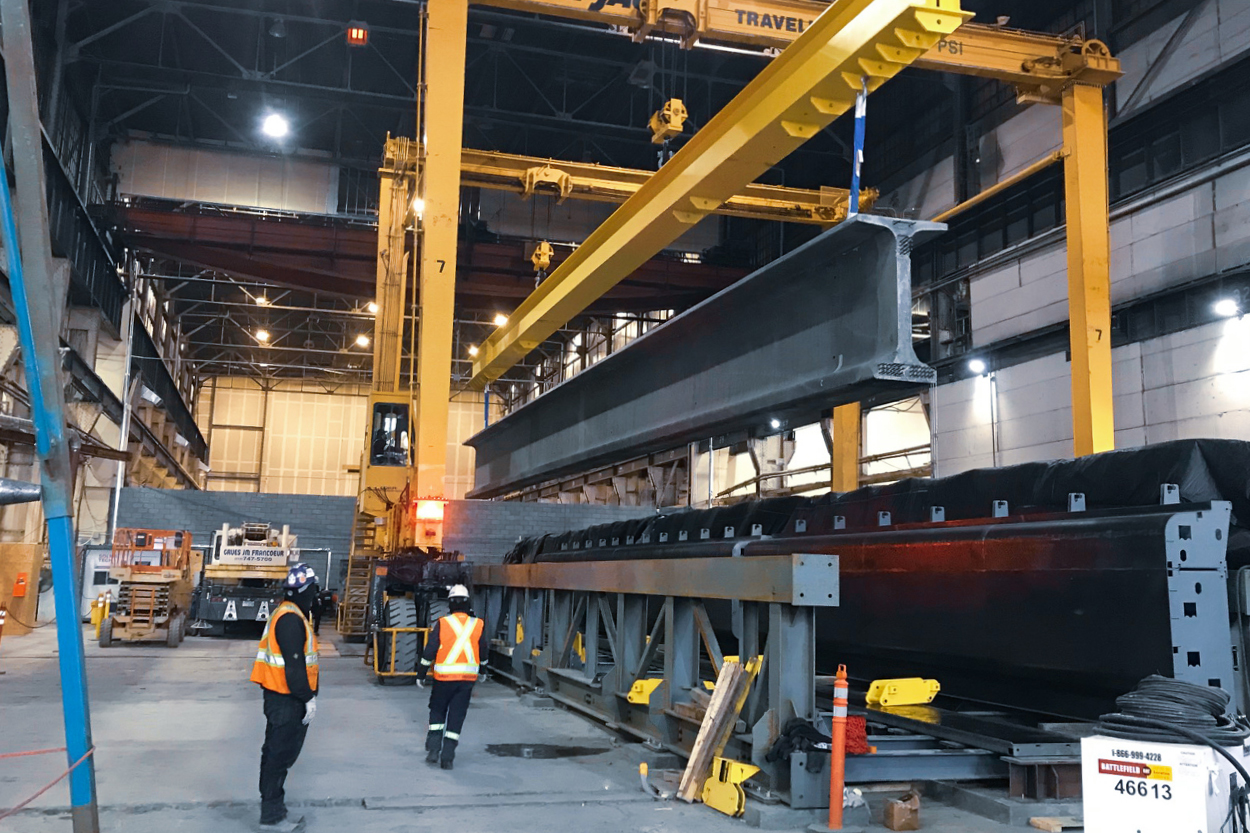
Two beams per day
The NouvLR workshop began activities at the end of February and will remain in service through the end of the year. With nearly 25 employees from all types of trades: carpenters, fitters, labourers, iron workers, crane operators, etc. Proper coordination between teams and their respective knowledge are critical when it comes to fabricating these concrete elements that have a 100-year durability requirement.
The goal is to produce 2 beams per day or 8 to 10 beams per week, according to construction needs.
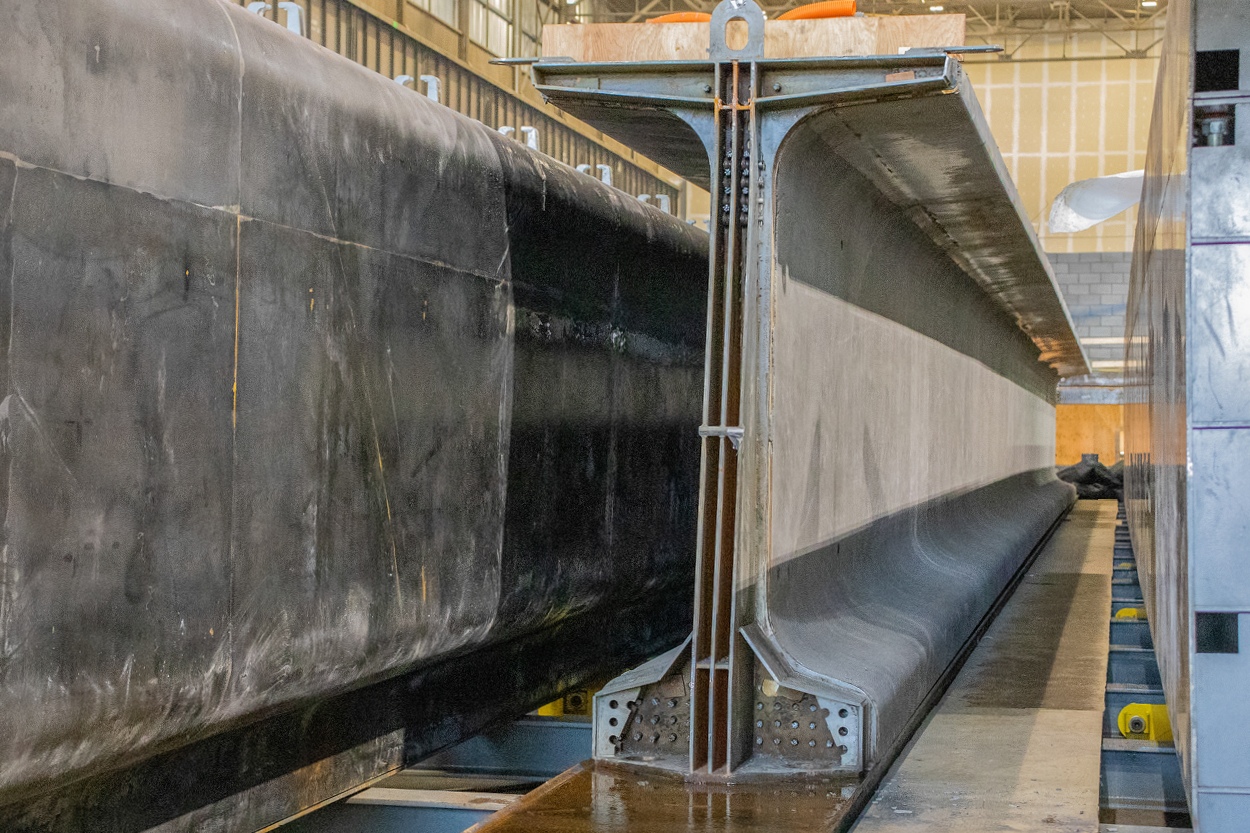
The typical process used to produce a beam is as follows:
- Placement of reinforcement
- Installation of post-tensioned cables
- Placement of parts to be embedded in the concrete
- Erection of forms
- Concreting of the beam, with concrete that was previously tested to validate durability
- Curing (concrete is heated and humidity maintained for 12-15 hours)
- Forms are stripped from the beam and post-tensioned cables are cut off
- Beam is moved to the plant's storage area
The process is repeated to make more! Stored beams remain at the plant for 3 days, i.e. the amount of time required for the concrete to cool. They are then hauled directly to the construction sites for installation.
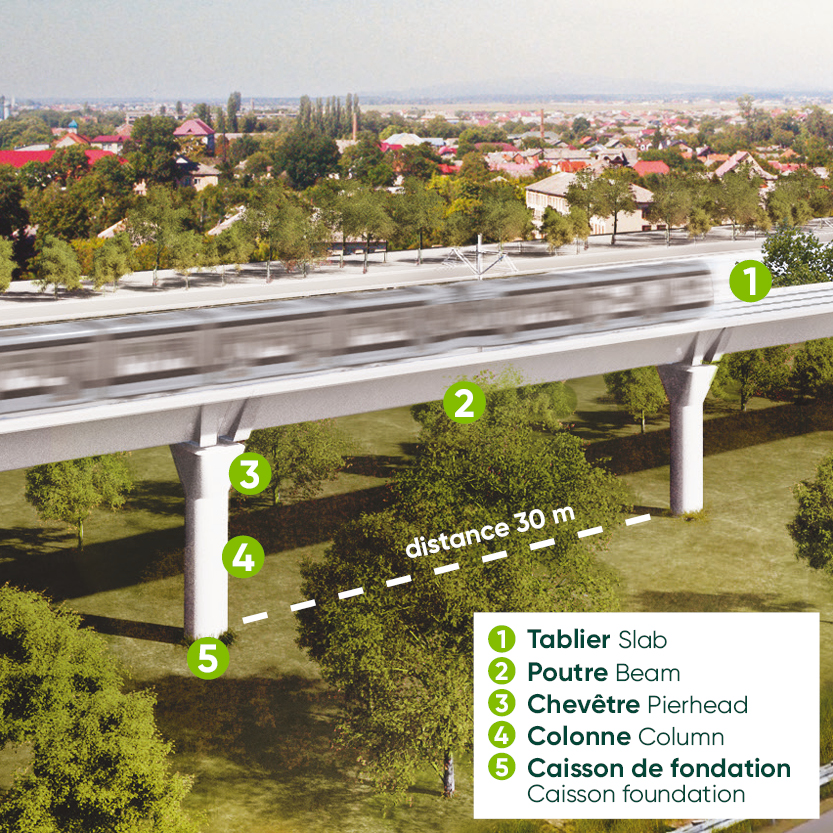
The goal is to maintain this rhythm throughout the year so that beams are not stored for very long at the workshop or on the site, and to keep work moving quickly.
NouvLR's NEBT (New England Bulb Tee) beams, in numbers
Number of beams: 276
Height: 2000 mm to 2200 mm
Length: 31 m to 36.9 m
Weight: 50 to 60 tons
Want more news? Follow the REM Twitter for more behind-the-scenes news
Nous sommes actuellement en phase de test pour s’assurer que le REM soit accessible pour tous et respecte les principes de l’accès universel. À suivre... pic.twitter.com/28NUvVQFQW
— REM - Réseau express métropolitain (@REMgrandmtl) 13 février 2019